Jakarta, KomITe.ID – The impact of an unplanned downtime is devastating and without a proper maintenance strategy in place, organization are exposed to these following risk: loss productivity, data loss, cost of recovery, client dissatisfaction and loss of corporate income.
Unplanned downtime not only impacts the company bottom line but there are also intangible costs to be considered, such as loss of business opportunity, loss of revenue, unproductive employees, decrease of share value, loss of trust from clients/partners, brand damage, loss of business to competitors, bad publicity/press.
Eugine Yaw, Senior VP Business, accompanied by Sunny Yaw, CEO PT TELEA Systems, along with advisor, Dr. Muchlis Ahmady on his visit with Rudi Rusdiah, Chief Editor Komite.id to TELEA’s comfortable office and warehouse in the heart of Central Jakarta, Thamrin City Tower.
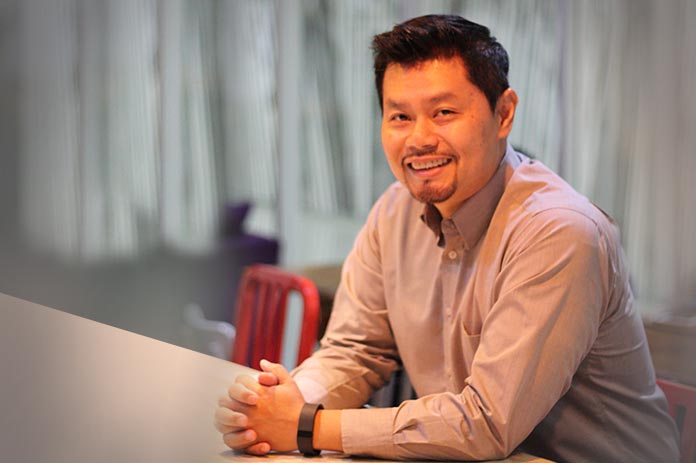
Causes of Unplanned Down Time
A study from Ponemon Institute shows that server downtime caused loss of 5,600 USD = IDR 76,000,000 per minute due to unplanned downtime or an equivalent to 42,000 USD = IDR 567,000,000 per hour. According to Gartner, major reasons for unplanned downtime is when an enterprise doesn’t have contingency or maintenance strategy plan in place. IT Downtime cost is devastating and could result in lost revenue up to USD $ 26.5 billion according to The Business Value of Technology report, in Information Week.
Furthermore, Gartner data shows a global enterprise experienced a downtime of 87 hours in a year. While a power outage cost them $ 46 million per year. The impact of unplanned downtime is enormous.
In the digital era now, all our daily routine had been digitized and the percentage of manual work has been decreased year by year. Unplanned downtime is impacting organizations in a various way includes employee’s productivity where employees don’t have the access to serve their client. Without a proper maintenance strategy, organizations are putting their corporate brand in stakes where dissatisfied clients will rage their disappointment in social media and these could take years to regain confidence and trust from the client again.
According to Forrester Research Inc., there are three significant causes of unplanned downtime, operational failure, natural disaster, and human error. Three (3) major causes of downtime that affect the organization are: First, caused by electricity failure (43%), second, damage in the hardware (31%), the third is network failure (16%). If there is no well-planned maintenance and life cycle (IT Maintenance and Life Cycle) strategy. The cost of recovering from an unexpected hardware failure is huge, especially when the hardware is approaching the end of life (EOL) / end of sales (EOS) / EOSW (end of software), where the availability of certain spare parts is rare. (See Table Downtime).
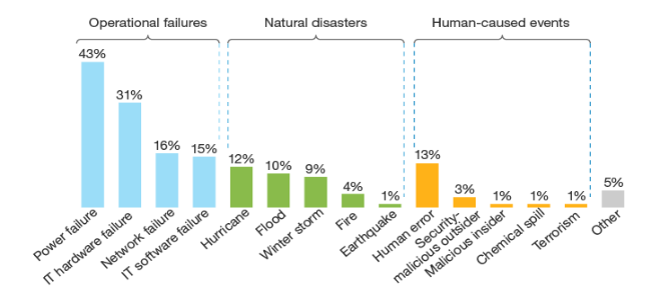
Impact of Unplanned Downtime
Based on survey data above, downtime can cause substantial losses for companies. According to a case study in July 2016, Southwest Airlines experienced an outage on one of its routers, they had been forced to shut down the entire system and reboot. This process took more than 12 hours and resulted in about 2300 flight cancellations. Losses from flight and vouchers cancellation reached at least US $ 25 million, according to the Dallas Business Journal. Additional losses include employee overtime, hotel accommodation and meals for dissatisfied travelers. This incident has caused a huge loss that is close to USD $ 54 million and this has not included the intangible cost of reputation damage.
Whereby in Indonesia, with the two recent downtime incidents which is not reported publicly, which is in Bank Indonesia and two power outage downtime at Soekarno – Hatta International Airport. Nothing has been made public on the root cause and the specific number of loss due to the unplanned downtime, but if we see from the results of Southwest Airline’s case studies above there is likely to be a considerable impact to the organization.
TELEA’s IT Maintenance & Life Cycle Strategy
To prevent unplanned downtime, TELEA recommends organizations to implement IT Maintenance and Life Cycle Strategy as below:
- Prevent
Proactively doing regular preventive maintenance in the data center to ensure the systems are up and running.
- Replace
Ready spare parts which are consigned and stored in client data centers, to reduce the delivery lead time that prolongs the downtime.
- Swap
One-to-one replacement unit from warehouse or ready-to-consign unit to be delivered to client’s data center. This could prevent one point of failure, just like router failure case studies from Southwest Airlines.
- Upgrade
Upgrade the hardware with pre-owned units that have been tested for 2-3 years in the market for reliability and compatibility that can provide stability to your datacenter.
With these Four IT Maintenance and Lifecycle strategy, Prevent, Replace, Swap and Upgrade. IT unplanned downtime could reduce to the minimum. This helps organizations to prevent unplanned downtime that causes billion dollars of lost and potentially reputation damage.
TELEA’s Data Center Uptime Solution
How TELEA could help to implement the 4 (Prevent, Replace, Swap, Upgrade) IT Maintenance & Life Cycle Strategy into your organization?
- Managed Services for implementing – PREVENT
Our expert technicians are ready 24/7 to perform routine check or remote support. Clients do not need to hire extra technician or headcount each month to perform routine checks. TELEA provides ticketing helpdesk, on-call service or in-residence service to be placed in client data center or in client office. This is our preventive and corrective maintenance helping clients to prevent unplanned downtime in their data center.
- Ready Parts for implementing – REPLACE
Once client’s data center is audited, TELEA will immediately order all spare parts based on the requirements. All spare parts are ready and available in the local warehouse in Indonesia which are available immediately to be replaced.
- Parts Consignment for implementing – REPLACE
TELEA provides spare parts that are ready to be consigned to client data center which can be replaced immediately by their technician.
- One to One Replacement for implementing – SWAP
TELEA provides one to one replacement unit that is ready which can be consigned to client ‘s data center. When there is a failure, the unit can be replaced immediately to prevent single points of failure.
- Pre-Owned Hardware for implementation (UPGRADE)
TELEA’s pre-owned units have been tested in the market for hardware and firmware reliability. Each hardware undergoes rigorous quality testing by meeting TL9000 and ISO standards 9001:2008. This ensures that all our preowned unit are reliable when it is implemented, thus reducing potential chances of hardware failure.
Improving Data Center Uptime
TELEA pushes the boundaries to improve data center uptime by providing:
- Extended Warranty
With extended warranty for major OEM brands, we can support your hardware until you don’t need it (10-15 years) and you will no longer need to worry about EOL/EOS End of Life /End of Sales.
- Multivendor
With TELEA global support, you could assure that you are getting the best service and support in our SLA (Service Level Agreement):
- Global Warehouse with USD 40 million (IDR 530 billion) spare parts available on TELEA’s Global Warehouse located in the US, Europe and Asia. Ready to support your multi-vendor data center needs.
- Global Support Team with multi-vendor certified engineer located in China, USA, Singapore and the Netherlands that are ready to support you 24/7.
Our clients have been with us for years and have been receiving significant improvement on their datacenter uptime. Just to name a few local and global clients Eurocars Group, SinemArt, Mazda, Sharp, ZTE, Nissan, Xerox, Oracle, AIA, Dell, Unilever had chosen TELEA as their most reliable partner. (*)